Cleanrooms belong to an exclusive group of areas with special requirements regarding infrastructure, environmental monitoring and staff competence and hygiene. Words by Patrycja Sitek, PhD, CRK owner
The increasing proportion of controlled environments in various areas of industry, is a source of new challenges for production staff and thus expectations on management to implement new standards. Digital Infrared Thermometer
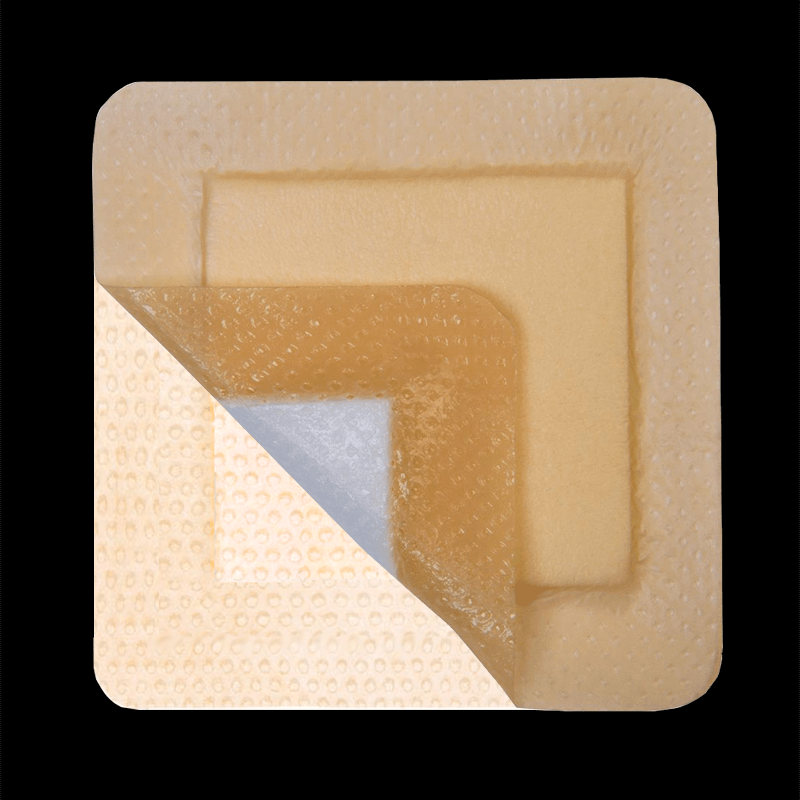
Various data indicate that more than 80% of all microbiological incidents and dust cleanliness exceedances are generated by the presence and activities of personnel in clean rooms. In fact, the process of entry, changing, handling of starting materials and equipment generate the release of large quantities of particles and, consequently, the transfer of biological agents from the skin surface and materials to the environment. Also, equipment such as tools, cleaning agents and packaging materials have a significant impact on clean room functioning.
Since personnel are the largest source of contamination in the cleanroom, it is important to ask how the transmission of animate and inanimate particles can be effectively reduced so that the requirements of ISO 14644 can be met in the personnel transfer process to the cleanroom area.
The use of specialised clothing prevents the dispersal of particles and microbiological agents from the surface of the worker's body into the surrounding production area
The most important element in preventing the transmission of contaminants in cleanrooms is the selection, appropriate to the cleanliness class, of dust-free clothing. In this publication, we will focus on reusable garments up to ISO 8/D and ISO 7/C classes, indicating the requirements for materials, surface breathability, specific design.
However, before we look at the requirements for cleanroom clothing we will briefly discuss the basic requirements for ISO8/D and ISO7/C cleanroom class personnel.
Firstly - in order to effectively prevent the transmission of contaminants into cleanrooms, detailed SOPs (Standard Operating Procedures) describing the basic principles of cleanroom operation in an organisation should be developed and implemented in every cleanroom. Such procedures should be written in the native language, implemented, understood and followed by the users. Equally important in preparing for work is adequate training for personnel responsible for the operation of the controlled area, as well as requirements for the provision of medical examinations appropriate to the hazards identified in the workplace. The possibility of random checks on the cleanliness of staff's hands, tests for the carrying of infectious diseases or even periodic dental check-ups are just some of the 'pleasures' awaiting those starting out in the cleanroom.
The basic requirements for maintaining good clean preparation hygiene include:
The entrance process to the cleanroom takes place through airlocks, which are designed and equipped to prevent cross contamination, especially crossing the paths of those entering. Depending on the type of production - we divide the airlocks according to increasing cleanliness classes or add an air shower airlock to the cleanroom.
Despite the rather liberal requirements of the ISO 14644 standard for rooms in ISO 8 and ISO 7 cleanliness classes, the level of pollution control remains high. This is because, with high reference limits for particulate and microbiological contaminants, it is easy to get the impression that we are in control of contamination all the time. This is why it is such an important part of the Contamination Control Plan to select the right clothing for the job that meets expectations not only in terms of comfort, but also in terms of construction, material characteristics, and breathability.
The use of specialised clothing prevents the dispersal of particles and microbiological agents from the surface of the worker's body into the surrounding production area. The most common material used to manufacture clean room clothing is polyester. This is because this material exhibits high anti-dust properties while being fully breathable. Importantly, polyester is an accepted material for the highest ISO cleanliness classes, as required by the CSM (Cleanroom Suitable Materials) agreement of the Fraunhoffer Institute.
Carbon fibres are used as an additive in the production of polyester clothes used for clean rooms, providing additional anti-static properties. Their amount usually does not exceed 1% of the total weight of the material.
Interestingly, although it may not have a direct impact on contamination surveillance, choosing the colour of the clothes according to the cleanliness class allows work discipline and control of staff movement within the cleanroom area.
Clothing dedicated to the cleanroom should, according to the requirements of ISO 14644-5:2016, not only retain particles from the worker's body, but, just as importantly, be breathable, comfortable and not easily fragmented.
Part 5 of ISO 14644, in Annex B, provides precise guidelines for function, selection, material characteristics, cut and finish, thermal comfort, requirements for the washing and drying process and also for clothing storage.
In this publication, we will introduce you to the most common types of cleanroom clothing that meet the requirements of ISO 14644-5.
Importantly, clothing up to ISO 8 class, commonly referred to as 'pyjamas', should be made, like a suit or a gown, of polyester supplemented with carbon fibres. The cap used to protect the head, can be disposable, but usually its functionality is reduced due to its susceptibility to mechanical damage. It is then worth considering the use of a reusable cap.
An indispensable part of the clothing is footwear, which, like the clothing, should be made of material that is mechanically resistant and resistant to the release of contaminants. This is usually a rubber or equivalent material that meets the requirements of ISO 14644.
The clothing should have the following finishing and material features:
In any case, if indicated by a risk analysis, protective gloves are worn at the end of the dressing procedure to maximise protection against the transmission of contaminants from the worker's body to the production area.
In the case of reusable clothing - once it has been used - it is sent to a cleanroom laundry, where it undergoes washing and drying processes under ISO 5 class conditions.
As no post-sterilisation of the clothing is required for ISO 8 and ISO 7 classes - immediately after the clothing is dried, it is packed and sent to the user.
Disposable clothing is not subject to the washing and drying process which necessitates its disposal and the establishment of a waste policy within the organisation.
Reusable clothing can be used between 1-5 days, depending on what has been established in the Contamination Control Plan following a risk analysis. It is important to remember not to exceed the maximum time for safe use of clothing, especially in production areas requiring microbiological contamination control.
Properly selected clothing up to ISO 8 and ISO 7 classes can provide an effective barrier to the transfer of mechanical and microbiological contaminants. However, for this to happen it is necessary to refer to the requirements of ISO 14644, carry out a risk analysis for the production area, develop a Contamination Control Plan and implement the system with appropriate employee training.
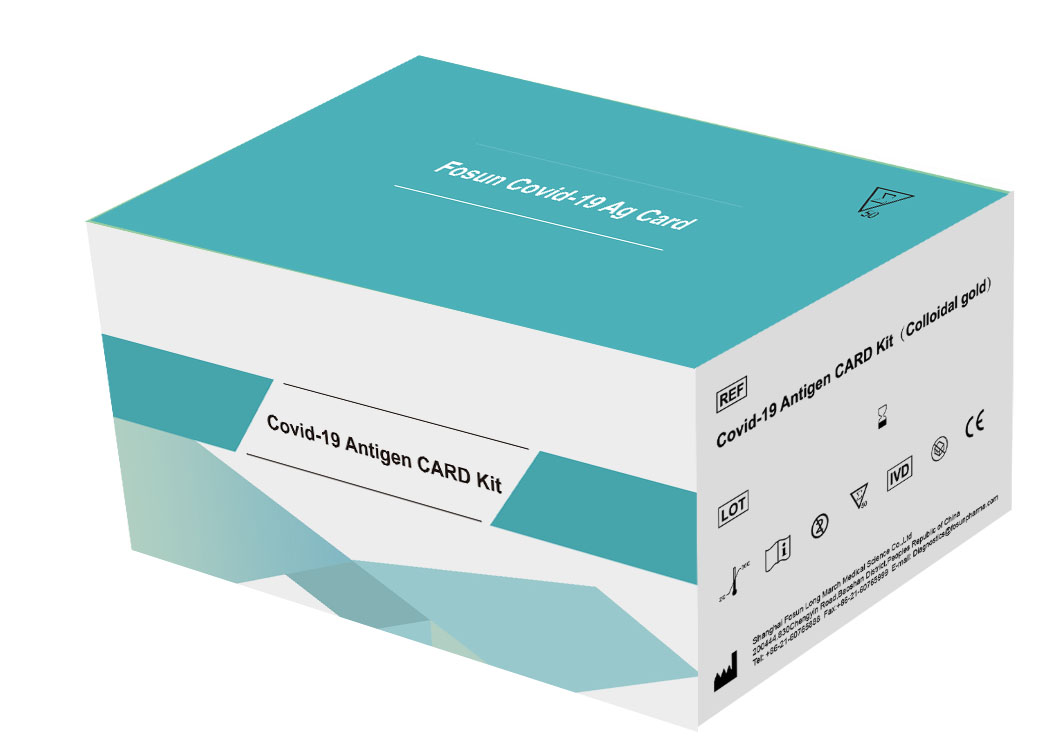
Wound Plaster With Even the best material and the finest technology will not perform adequately if a system of internal and external training is not implemented in the organisation to ensure that an appropriate level of awareness and responsibility is developed in adhering to the Pollution Control Plan.