Cavitation results from excessive vacuum conditions at the inlet to a pump. High vacuum creates vapour bubbles within the oil, which are carried to the discharge (pressure) side. These bubbles then collapse, resulting in cavitation. Such operating conditions can create an implosion because of fluid compression.
Kevin Walker from Hydrasales Cape Town technical support explains that cavitation causes gradual metal erosion, typically on the sealing surfaces of the components in the pump, resulting in an increase in contamination levels in the fluid. The cavitation becomes the source of contamination, and this is invasive. Repair or replacement of pumps can be expensive. However the damage is not localised to the pump. Fragments from deteriorating pump components can have a catastrophic impact down the line as a result of particle contamination; worse still, pump failure can result in damage throughout the system and require a complete system flush and further repairs. Gas Coalescing Filter Elements FG-36 JFG-36
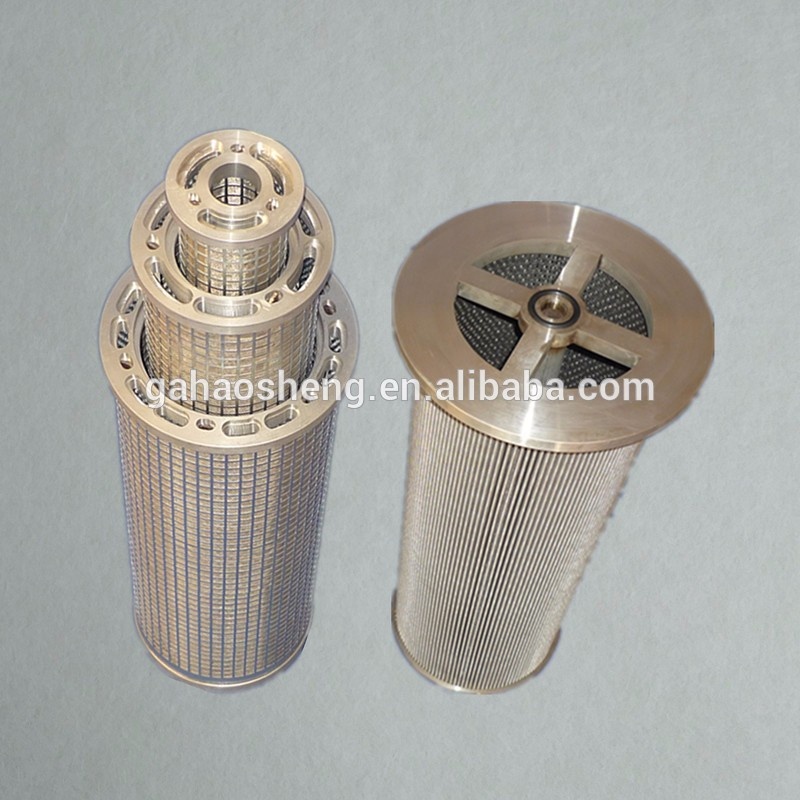
In recent times, more and more system designers are including high- pressure inline filters for this reason. “Contamination creates undue wear on other components, which eventually leads to high levels of dirt infecting the system and results in ultimate system failure,” explains Walker. When investigating a system in operation, obvious symptoms of cavitation include noise and vibration. When air bubbles implode, they can make a series of bubbling or cracking sounds. In addition to the noise, there may be unusual pulses and vibrations in the hydraulic line not normally experienced. Here are some of the consequences:
Clogged suction strainer or filter: Results in excessive heat.
Leakage on pump inlet lines: Results in increased system contamination.
Restricted or choked suction line: Results in violent implosion.
High start-up viscosity (low temperature): Results in reduced lubrication.
Rapid increase of pump volume demand: Results in friction and wear.
Hydrasales and MP Filtri offer a fully comprehensive filter sizing programme to allow for both contamination control and oil feed as per pump specification, as well as offering the Automatic Particle Counter to monitor and confirm cleanliness levels to the ISO 4406 standard.
Suction strainers are an inexpensive way of protecting a pump from larger particulates, with common industry standards being 60 µm, 90 µm, or as large as 250 µm for high-viscosity fluids. These can be supplied with a magnetic column or bypass feature for cold startup or clogging. However if these filters are not serviced regularly, they can either starve the pump of oil when clogged (cavitating) or remain in bypass (not filtering).
Wire mesh spin-on elements (cans) are seen frequently in the marketplace, but the element itself is costly and it is not reusable. MP Filtri’s SFEX Elixir range allows for a head with the bowl and a removable cartridge. This allows wire mesh cartridges to be washed and re-used like a suction strainer. The housing includes bypass, eliminating the possibility of oil starvation, as well as either visual or electrical clogging indicators for maintenance scheduling.
With the Spin-On range, Hydrasales further offers conventional spin-on elements as well as single or double heads for higher flow rates with both visual and electrical clogging indicators. These can be cross-referenced against most brands. In addition, the FAS series filters are designed for a variety of filtration requirements for suction applications. The design of these filters allows them to be mounted semi-immersed in the reservoir or inline. This inline option can accommodate higher flows than the aforementioned SFEX.
The SF Range comprises a semi-submerged positive head suction filter with tank side or bottom mounting. It features an anti-drain valve allowing the filter element to be changed without draining the tank. An optional magnetic column captures ferrous particles. These filters are available with or without bypass and accommodate flows up to 800 l/min with visual or electrical clogging indicators.
Pump cavitation can be a curse, giving rise to system breakdowns, costly repairs and loss of productivity. System designers must take the proper steps at the design stage, and ensure correct reservoir design that includes line and filter placement as well as filter sizing to ensure optimal oil delivery. The inclusion of condition monitoring to achieve the correct cleanliness levels will result in longevity of the pump, with minimal downtime and costly maintenance.
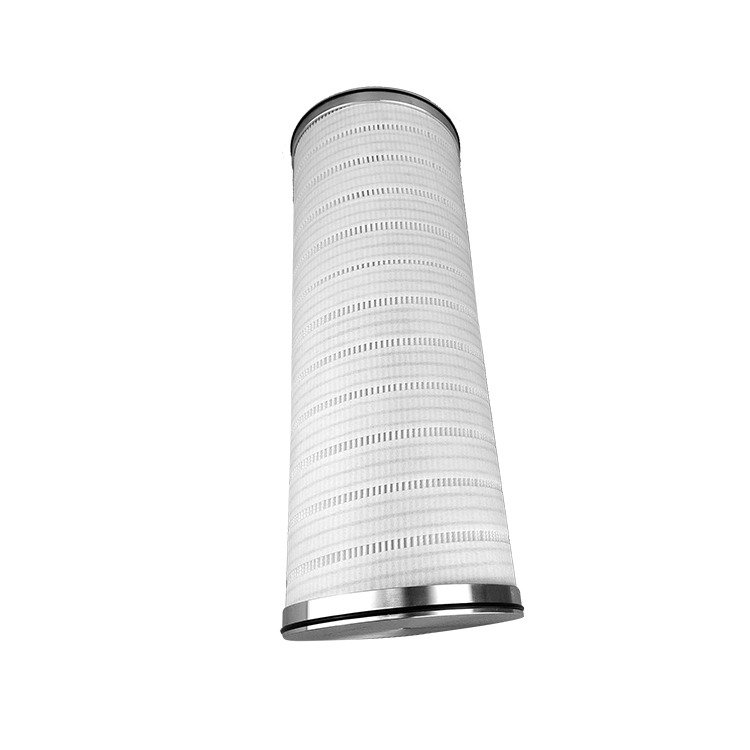
Parker Filter Elements © Technews Publishing (Pty) Ltd | All Rights Reserved